
With a Ph.D. in Concrete Materials I specialize in "green" concrete, but have an affection for all things concrete. This blog will detail my exploits into all things concrete for the home.
Wednesday, December 9, 2009
Concrete that looks like, asphalt?
A month or so ago Studiobuild was contacted by a Ferrari race team to make a couple trophies for their series championship. The catch was they wanted the bases made out of asphalt. Besides my aversion to asphalt, the logistics of an asphalt trophy just didn't' work. So I suggested the next best thing, a concrete base the looks like asphalt. Jerad made the mold and I went to work on the mix. I took a superpave asphalt mix design and substituted black cement paste with appropriate viscosity for the liquid binder. I even compacted them with a Marshal hammer. After coating with a high gloss sealer, the results look just like asphalt. Never thought I would imitate asphalt with concrete, but it worked quite well.

Monday, November 23, 2009
Friday, November 20, 2009
Sealing the Concrete Buffet Top
I have been falling behind on blog posts with our house being on a homes tour, traveling, and school. Meanwhile the concrete buffet top has been sitting and waiting in the garage. Pretty much all of the finish work has been completed so it getting old didn't impact grinding. Although at this point there isn't anything you could do other than burn up pads.
Here is a shot of the crushed Murano glass in the surface. The big pieces are all back-lit with fiber optics.
Thursday, October 8, 2009
Buffet Top Reveal
The stripped buffet mold. The flowable concrete produced a very smooth texture with very few bugholes, just a couple on the edge.
Sunday, October 4, 2009
Placing the Fiber Optic Concrete
The fiber optic buffet mold has sat covered in the garage for a couple weeks due to some other more pressing things. Today I got back to it.
Finished gluing the fiber optics in.
Some of the first ones came loose. The ones in the mold were fine but the ones glued to the glass pieces came off. I used more hot glue on this round and everything seemed to hold better.
Here are the specs:
- 2.5:1 sand to cementitious materials,
- 5% metakaolin clay,
- 0.4 water-to-cement ratio,
- 1:1 latex admixture to water,
- 3 pcy cellulose microfibers,
- 1.5 pcy polypropylene fibers, and
- a ton of high-range water reducer
I have had problems in the past with the cellulose fibers not dispersing in mortar mixes due to the lack of coarse aggregate. The sand, water, and fibers mixed for 10 minutes before starting to mix the concrete. That seemed to get everything broken up correctly.
Thursday, September 10, 2009
Fiber Optic Concrete Progress
The mold construction for the fiber optic bar/buffet top is coming along. I taped off the bottom, drew an abstract shape, cut out the shape, and glued in crushed glass. I almost cried while making the crushed glass out of a broken Murano glass lamp from Italy. It even had the master's signature but was unsalvagable as a lamp. The bigger pieces were glued in with a drop of epoxy and the little pieces sprinkled on after spray adhesive. What is the weird frame you ask, hold tight.
Tuesday, September 8, 2009
Fiber Optic Illuminated Concrete Bar Top Project
The next concrete project is underway. This is a top for a bar/buffet. The concrete will be regular grey with crushed Murano glass and fiber optics.
The mold is pretty standard construction, 3/4" melamine with caulked edges. I only had white caulk so it blends in. The dimensions are 62"x13"x2".
The shape of this piece is pretty straightforward, however I am trying a few new techniques on this one. An abstract shape was drawn on painters tape and removed. Spray glue will be used to seed the red crushed glass in this pattern. The fiber optics will be glued to the back of the crushed glass in this section so the shape will glow through the glass.
Thursday, September 3, 2009
Sunday, August 23, 2009
Finished: White Concrete Desk Project
The white concrete desk is completed and installed. The cobalt blue and green bottles with the white sand and cement really pops.
Sunday, August 9, 2009
Finishing the White Desk
The white concrete desk was placed two weeks ago. Form were stripped after 4 or so days. Initial grouting was done at 4 days and moist cured. Initial grinding 50 and 100 grit was done at 7-days. A second thinner grout was applied with a rubber trowel. The countertop was moist cured for another 7-days until polishing. At 14 days after placing the top was polished through 1500 grit. So the full polishing scheme went 50, 100, 200, 400, 800, and 1500. I skipped 3000 grit since the sealer doesn't really stick to it. Four coats of sealer went on today. The sealer will cure for another day (it is really hot and humid in the garage right now) and will get waxed before installation.
Monday, August 3, 2009
Desk Progress
Thursday, July 30, 2009
White Concrete Desk Reveal
One of the characteristics that helps lighten white cement is fine grinding, even finer than Type III high early strength cement. I will vouch for that. This countertop was hot to the touch 6 hours after placing. Good news is that it can be finished much sooner.
The desk proved difficult to strip the forms since the aggregate was glued in place. The glass stayed in placed and was well distributed across the surface. In this picture I started slurry coating the surface to fill the holes left from the curved part of the glass. In a day or so it will get a grind with 50 grit and then another slurry coat.
Monday, July 27, 2009
Placing the White Desk
To get the colored glass, blue and green wine and beer bottles were soaked in water to remove the labels then crushed and rewashed. The mold was sprayed with glue to hold the glass in place.
Saturday, July 25, 2009
White Desk Project
Everything has been prepared for the white desk. The mold is a pretty standard construction. I had some leftover MDF so I used that and spray painted to seal the wood. The desk has a thickened front edge to cover the in-place frame.
The desk will be white concrete with crushed glass in the surface. I saved some good blue and green bottles. First they were soaked in water to remove the labels, then crushed with a hammer to the appropriate size. Beer bottles can be problematic if not cleaned properly. The sugars in the beer tend to retard the concrete set. These were washed again after crushing.
How do you make white concrete, mmm use white cement. This is a little harder to track down for the average person since Home Depot doesn't carry it. Masons and stucco guys use white cement or call your local decorative supplier. This cement and sand was donated by Mike Murry at Decorative Concrete Supply. The only real difference between white and regular Portland cement is they leave out the tetracalcium aluminoferrite. It is a small part of regular cement that doesn't really contribute to strength.
Another concern for making white concrete is the aggregate. Regular sand tends to make the white cement concrete a tanish color. You can buy pure silica sand (ash tray sand) at local suppliers. Since this is a small desk, shrinkage isn't really a concern so a mortar mix is appropriate.
The mix will be a standard mortar mix; 2.5:1 sand to cement, water-to-cement 0.40, 10% metakaolin clay, high range water reducer, viscosity modifier, latex, polypropylene fibers, cellulose fibers, and de-air entraining agent. The total batch will be 1.0 cf.
Wednesday, July 8, 2009
White Concrete Desk Project
Since the last project was black, time to do something white. We built a closet in our guest bedroom and left room between the window and the closet for a built-in desk. The room is green with orange accents and blond birch trim. The plan is to build a white concrete countertop for the desk with exposed blue and green recycled glass.
Below is the black fireplace with the slate tile and new carpet.
Friday, June 19, 2009
KC Home Design Awards
Here are a couple pictures of the awards I have been studiobuild with for Kansas City Home Design Magazine.
The concrete/mortar for the regular awards has a little higher paste content than normal with a little silica fume for higher strength. There is also a ton of non-chloride accelerator so we can demold them quickly. They achieve over 4000 psi in four hours.
The Ed Tanner awards are 100% crushed glass (beer bottles from my garage) with a blend of slag and fly ash. Since there is no cement, the slag was heat activated to achieve the desired strength.

Thursday, June 4, 2009
KC Home Design Awards
Although I can't show any pictures yet, recently I have been assisting StudioBuild making awards for the KC Home Design Magazine Design Excellence Awards. There are first, second, and third place awards in 17 residential and commercial categories such as "Outdoor Spaces." The awards are a combination of concrete and wood. A special concrete mixture was designed that achieves over 4000 psi in 4 hours and will have an ultimate strength above 20,000 psi. Since the awards are not a typical concrete shape, the ultra high strength will keep them from breaking should someone drop theirs.
Saturday, May 23, 2009
Equipment Upgrade
Sunday, May 17, 2009
Fireplace Results
The fireplace surround is done. It took longer than expected because I couldn't seem to get just the right black color. The concrete itself was black then I acid stained it black again. That still wasn't as jet black as I wanted so I used a couple coats of a very strong dye. Once the dye dried I sealed it with an acrylic. Since no one will be eating off of it, hopefully, the sealing materials don't have to be food-grade.
Before
After, a little taller and wider and filled in that weird gap near the wall.
One layer of tile will go around the fireplace and then a stainless steel insert and fireglass.
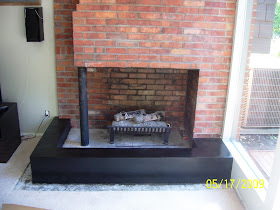
Monday, April 27, 2009
Fireplace Surround Progress
Here are the finishing steps and the current progress;
1. Strip the forms
2. Thick slurry coat to fill the large bug holes
3. Quick grind 50 grit through 200 grit (about 30 minutes)
4. Light slurry coat
5. Quick grind quick grind 200 grit through 400 grit (about 30 minutes)
6. Spot slurry as places that are still low
7. Finish grind at 400 grit (about 30 minutes)
8. Seal and wax
9. Lightly rub with steel wool to remove the shine